About Us
Atlas Organics, a Generate Upcycle company, provides the highest quality finished compost to residential homes, corporations, local businesses, and municipalities throughout the country. We provide compost for use in agriculture, landscaping, golf courses, and gardens.
Mission
Atlas Organics exists because we believe that people can and should contribute to something greater than themselves. Our goal is to become the greatest organics recycling service in the world through providing access to composting for more homes, companies, and municipalities than ever before!
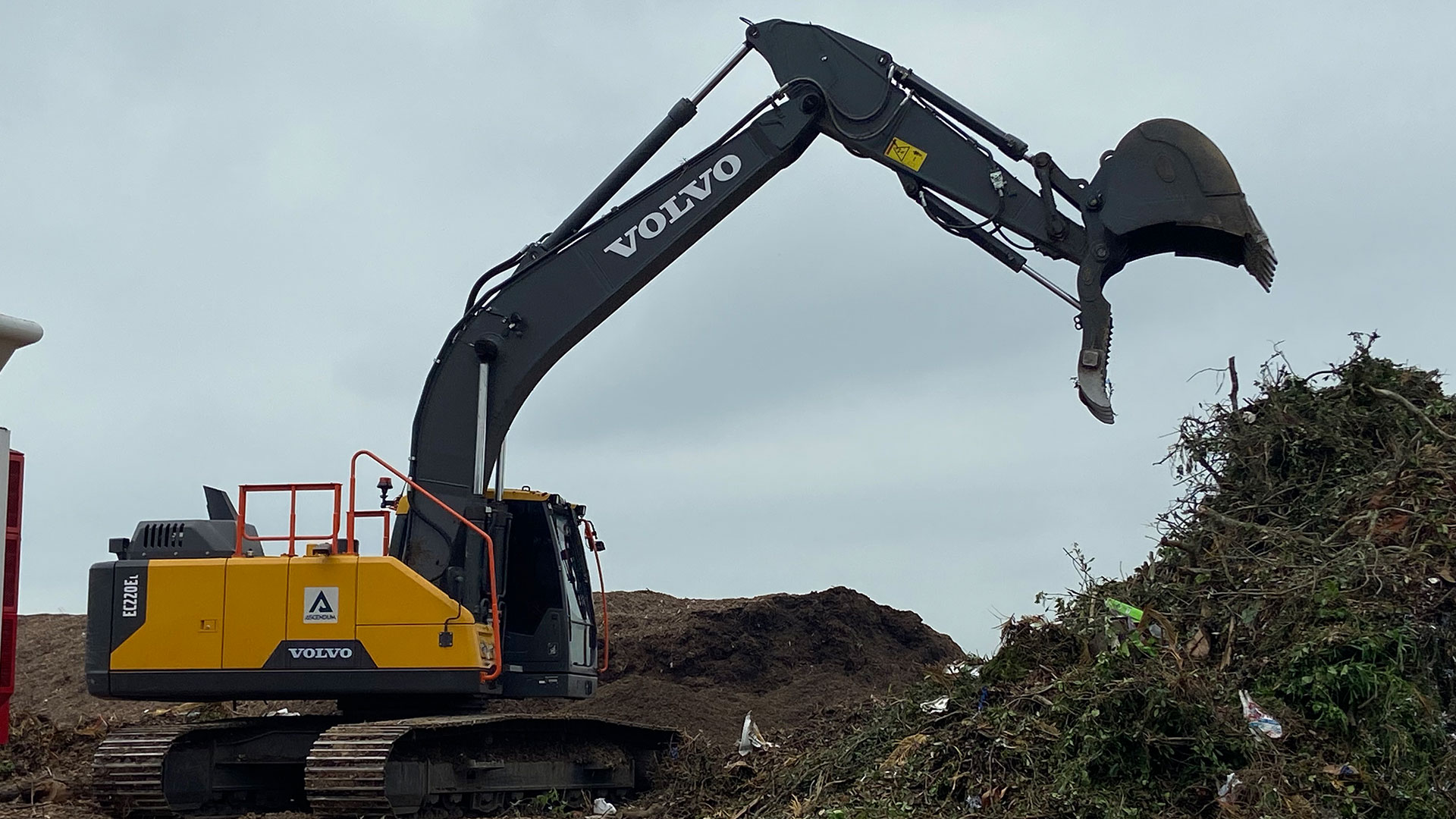
Our Process
Atlas Organics manages and processes a variety of organic waste products including yard waste, food waste, and biosolids at various facilities. Our typical process begins with the acceptance and grinding of yard waste utilizing horizontal grinders fed by excavators. These machines take loose unground municipally collected yard waste and reduce it in size to create single ground mulch. This material acts as a carbon source in the composting process. After the yard waste is processed, it is either added directly to the composting process or mixed with a nitrogen source such as food waste or biosolids at a ratio of approximately 50:50 by weight. This material is then added to the composting system made up of aeration blowers timers and temperature probes. All material movement on site is done through the utilization of wheel loaders.
Process images
What is EASP?
Atlas Organics utilizes Extended Aerated Static Pile (EASP) composting systems originally engineered by O2 Compost. With EASP composting, fresh air (with oxygen) is blown into the pile under positive pressure to maintain aerobic conditions throughout the pile, eliminate the need for pile turning, accelerate the decomposition of the organic waste material, achieve pathogen reduction requirements, and prevent generation of offensive odors. Compared to typical windrow composting operations, Atlas avoids using a diesel-powered windrow turner and avoids generating dust by avoiding pile turning, all while keeping optimal operating composting conditions to process material faster. Throughout the process the material is monitored using various quality control methods including batch protocol, bulk density, moisture, temperature, and Solvita.
Once the material is fully composted, it is removed from the composting system and screened utilizing a Powerscreen Phoenix 2100 trommel screen. This material is then tested by Soil Control Laboratories for nutrients, pathogens, metals, and other horticultural parameters using the US Composting Council Seal of Testing Approval (STA) program. After results are analyzed to confirm regulatory limits are met, the material is sold into the marketplace.
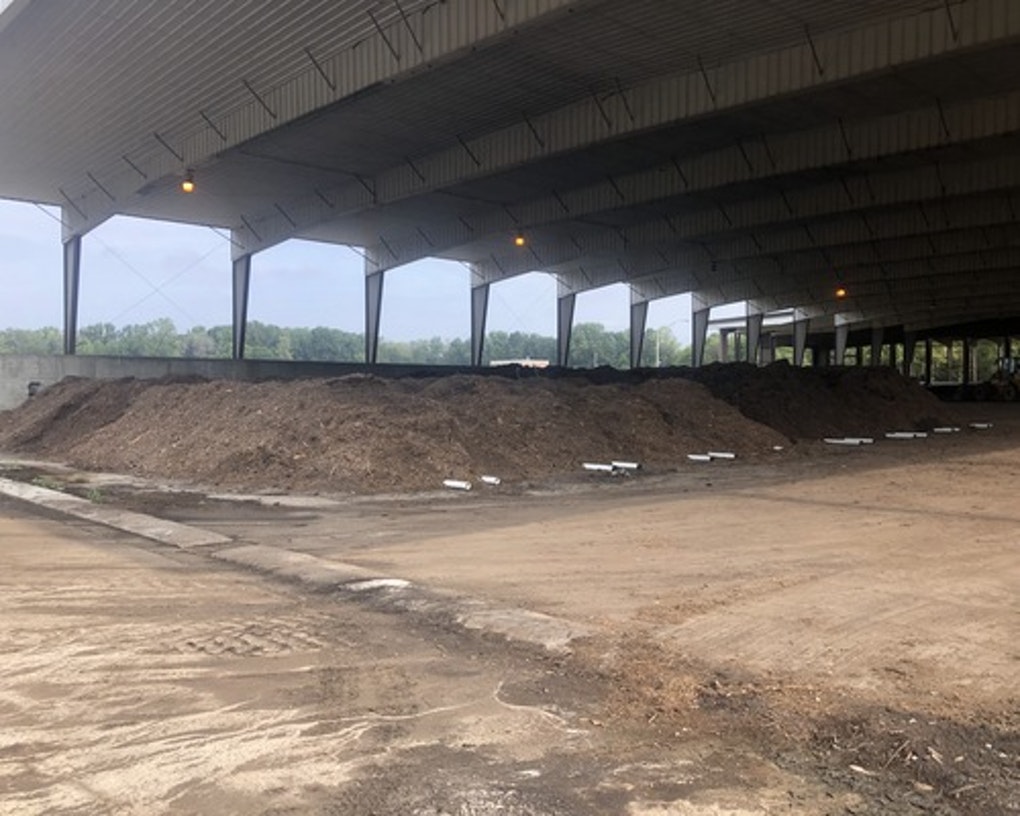